Blog CEKARE #2
The 5S Method
By Baptiste CARRE, 26/03/2025.
Time to read : 5 min
Have you ever found yourself in a situation where you couldn't find what you needed, right when you needed it? Whether it's a misplaced tool in a workshop or a missing file in an office, these moments of disorganization can lead to frustration, wasted time, and even potential hazards. The impact of a disorganized workspace can be significant, affecting productivity, costing money, and sometimes leading to dangerous situations.
Fortunately for you, there's a straightforward and effective solution to these challenges: the 5S method.
SUMMARY
What is the 5S method ?
The 5S method is a systematic approach to creating and maintaining an organized, clean, and efficient workspace. Originating from Japan, it is a cornerstone of lean management, which focuses on maximizing value while minimizing waste. The 5S method was developed as part of the Toyota Production System (TPS) in the 1950s, aimed at improving efficiency and reducing waste. Over time, it has been adopted globally across various industries, from manufacturing to healthcare, due to its simplicity and effectiveness. The method is not just about tidying up; it's about creating a culture of continuous improvement and engagement.
5S represents Japanese words that stands for :
Seiri - Sort
Seiton - Set in Order
Seiso - Shine
Seiketsu - Standardize
Shitsuke - Sustain
Applying the 5 S method in your business has numerous advantages such as :
Boosts Efficiency: With everything in its place, you spend less time searching and more time doing.
Enhances Safety: A clean and organized workspace reduces the risk of accidents and errors.
Improves Quality: Standardized processes lead to consistent and high-quality outputs.
Increases Morale: Employees thrive in a well-maintained environment, leading to higher job satisfaction.
Saves Money: Reduced waste and improved efficiency translate to significant cost savings.
Even if it was originally created into an industrial environment, the 5S method is renowned for its versatility. Whether you're in a bustling factory, a busy office, a healthcare setting, or even at home, 5S can be tailored to fit your needs. It's all about creating a space that works for you, not against you.
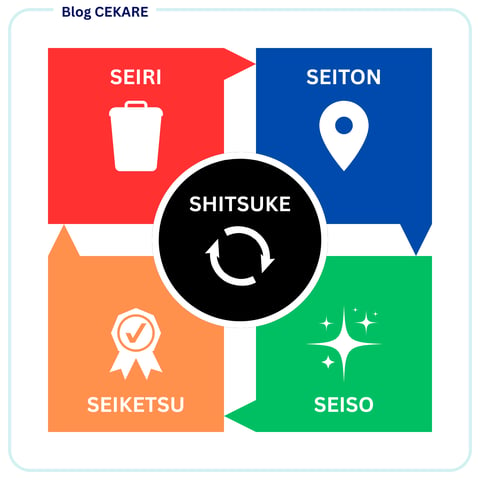
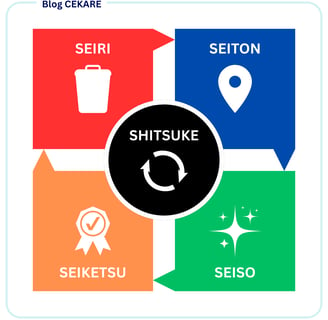
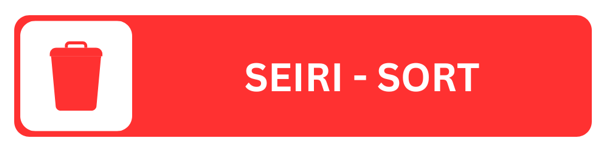
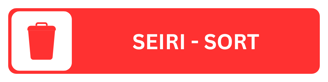
The Five Steps of 5S.
While applying the steps of 5S, always remember the following sentence :
“There is a place for everything and everything is in its place !”.
Sorting is all about decluttering. It involves going through everything in the workspace and removing unnecessary items. By eliminating clutter, you reduce the time wasted searching for tools and materials, making the workspace safer and more efficient.
“We don’t use it here, put it away!”
Example : In a manufacturing plant, this might involve clearing out old, unused machinery to free up space for current operations. In an office, it could mean removing outdated files and documents to make room for current projects.
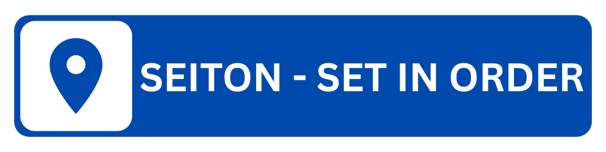
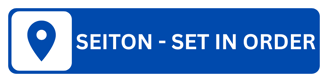
This step focuses on organizing the remaining items in a logical manner, ensuring everything has a designated place. An organized workspace makes it easier to find what you need, reducing frustration and improving efficiency.
“Make it visible and accessible, always!”
Example : In a warehouse, setting in order might involve arranging inventory in a way that optimizes picking and packing processes. In a retail store, it could mean organizing products on shelves to enhance customer experience and ease of access.
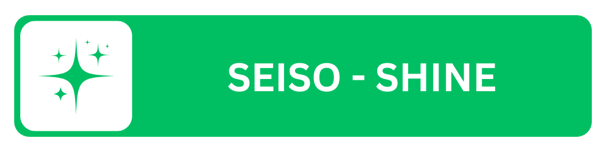
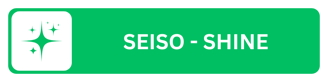
Shine is about maintaining cleanliness and inspecting the workspace regularly to ensure it stays tidy and safe. A clean workspace is not only more pleasant to work in but also safer, reducing the risk of accidents and errors.
“Cleaning is a part of your routine!”
Example : In a food processing plant, shining might involve regular cleaning of equipment to prevent contamination and ensure food safety. In a hospital, it could mean maintaining cleanliness in patient areas to prevent the spread of infections.
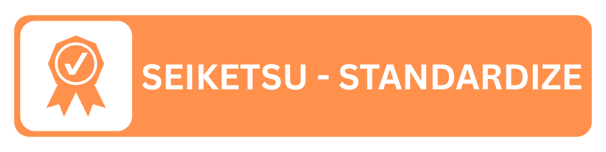
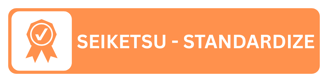
Standardizing involves creating standardized processes for maintaining the first three S's (Sort, Set in Order, Shine). This ensures consistency and sustainability in workplace organization.
“Always control if it’s cleaned and in order!”
Example : In an automotive assembly line, standardizing might involve developing procedures for tool maintenance and storage. In a call center, it could mean creating scripts and protocols for handling customer inquiries efficiently.
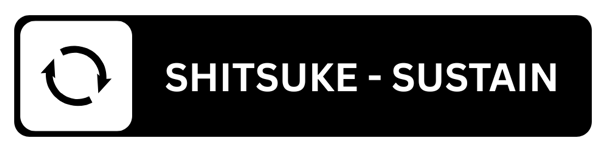
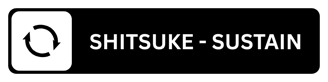
The final step focuses on sustaining the improvements made through the first four S's. Sustaining ensures that the gains achieved are maintained over time, fostering a culture of continuous improvement.
“Involve everyone,we are all responsible!”
Example : In a logistics company, sustaining might involve regular audits and feedback sessions to ensure adherence to standardized processes. In a software development firm, it could mean conducting periodic reviews of coding practices to maintain high standards.
How to apply the 5S method ?
Never start the 5S method alone, implementing 5S within your company involves dynamism and commitment from all your colleagues and will have to be supported by management.
Educate Your Team : Make sure everyone understands the 5S method and its benefits.
Start Small and Expand : Pick a pilot area to demonstrate the impact of 5S. Success here can build momentum for wider implementation.
Regular Check-ins : Conduct regular audits to ensure the 5S principles are being followed. Use visual aids and checklists to monitor progress.
Encourage Feedback : Create a culture of continuous improvement by encouraging suggestions from your team. Don’t hesitate to reward the ones that contribute the most.
Lead by Example : Ensure leadership is committed to the 5S method and provides the necessary support and resources.
Conclusion about the 5S method.
With the 5S method, you have the tools to create a workspace that's efficient, safe, and enjoyable to be in. If you need help getting started or want to take your 5S implementation to the next level, don't hesitate to reach out. Together, we can transform your workspace to support your goals and enhances your overall operations.
CEKARE
Boost your operational and industrial performance.
Mail : contact@cekare.eu
Phone : +370 663 58 502
© 2025. All rights reserved.