Blog CEKARE #1
Problem Solving : Methods and Tools
By Baptiste CARRE, 25/03/2025.
Time to read : 9 min
Every business faces challenges—whether it’s a production delay, a customer complaint, or inefficiencies in a process. But the real difference between successful and struggling organizations lies in how they tackle these problems.
In this article, we will embark on a comprehensive exploration of problem-solving, addressing the following essential topics:
Defining the core principles of "problem-solving."
Outlining the systematic steps involved in the problem-solving process.
Providing a comprehensive overview of well-known problem-solving methods and guiding you in selecting the best approach for various situations.
Introducing effective tools to enhance the efficiency and success of your problem-solving efforts.
SUMMARY
What is problem solving ?
At its core, a problem is a situation that presents a challenge or an obstacle, preventing you from achieving a desired outcome. In the context of a business or an organization, problems can manifest in various ways, such as inefficiencies in processes, quality issues, or failures in meeting customer expectations. Recognizing a problem is the first step toward resolving it, and it often involves identifying a gap between the current state and the desired state.
Problem-solving isn’t just about fixing issues when they arise; it’s about creating a culture where teams continuously improve and prevent problems from recurring. This mindset is the foundation of Lean Management and Continuous Improvement, helping companies stay competitive, efficient, and innovative.
Facing problems and resolving them will:
Enhance Operational Efficiency: By identifying and addressing inefficiencies, companies can streamline their processes, reduce waste, and improve overall productivity.
Drive Innovation: Problem-solving encourages creative thinking and the exploration of new ideas, leading to innovative solutions that can set a company apart from its competitors.
Improve Customer Satisfaction: Addressing problems promptly and effectively enhances the quality of products and services, leading to higher customer satisfaction and loyalty.
Empower Employees: When teams are equipped with problem-solving skills, they feel more empowered and engaged. This leads to increased job satisfaction and a more proactive approach to challenges.
Promote a Culture of Continuous Improvement: Effective problem-solving fosters a mindset of continuous improvement, where employees are constantly seeking ways to enhance processes and outcomes.
Mitigate Risks: By proactively identifying and addressing potential issues, companies can mitigate risks and prevent small problems from escalating into major crises.
Problem solving : Going step by step.
To resolve a problem you are facing, whatever the methodology you will use, you will follow a similar path.
Describe the Problem : Clearly articulate the problem. Go on the field, exchange with people involved in processes and collect facts. Identify what is the gap between the current situation and the expected situation. Asking yourself what's going wrong, and why is it important to fix?
Define Objectives : Set clear and measurable goals based on precise criteria - cost, time, quality, or criteria suitable for your business performance. What do you want to achieve by resolving this problem successfully?
Identify Causes : This step aimed to understand where the problem is coming from! Use tools like the 5 Whys and Ishikawa diagrams to uncover root causes. Keep asking "why" until you hit the core issue.
Identify Corrective Actions : Now that the causes are identified, brainstorm potential corrective actions with your teams. Select the most appropriate ones based on their feasibility and impact.
Apply Corrective Actions : Implement and execute corrective actions, start with the “quick-win” ones with immediate effect. Ensure everyone knows their role and communicates effectively to apply them.
Monitor and Adjust : Track the progress following the applications of the corrective actions using metrics and data. Make adjustments if needed based on feedback and results. Are the corrective actions working?
Standardize : Document your success and make it the new standard. Share your findings with other teams to replicate the improvement.
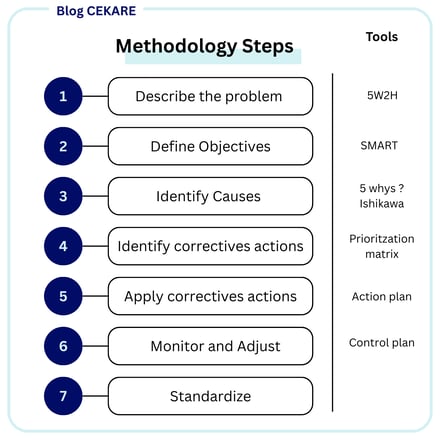
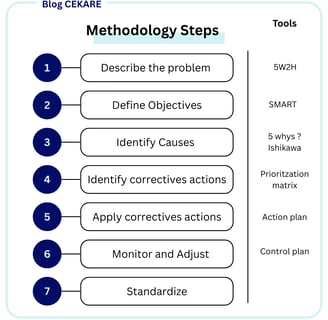
Which problem solving methods are commonly used ?
Problem-solving methodologies are widely used in lean management, let’s explore the ones used the most nowadays. They are all following the same logic, as described before, but with their own specificity to face different situations. Those proven methodologies have been developed by companies renowned for continuous improvement mindset such as Toyota, Motorola, General Electric.
DMAIC (Define - Measure - Analyze - Improve - Control)
DMAIC is used for improving existing processes based on data and statistical analysis (we will talk of lean six-sigma analysis).
Define : Clearly outline the problem and set your goals.
Measure : Collect data to understand the current situation.
Analyze : Find root causes using statistics tools and data analysis to find root causes.
Improve : Develop and test solutions. Which solutions provide the best results?
Control : Implement the best solution and monitor its effectiveness through a control plan.
PDCA (Plan - Do - Check - Act) or DEMING Wheel
PDCA is a simple and iterative method used to continuously improve processes and test changes.
Plan : Identify the problem and develop a plan, clearly listing objectives and actions.
Do : Implement actions of your plan on a small scale. How does it perform in a test environment?
Check : Analyze if the results meet the expected results. Did your plan work as expected?
Act : Standardize the improvements and make it as the new norm.
8D (Eight Disciplines)
8D is a structured, collaborative problem-solving method, often used in manufacturing.
1D - Use a Team : Assemble a diverse team to tackle the problem from all angles
2D - Describe the Problem : Create a clear problem statement.
3D - Implement and Verify Interim Containment Actions : Apply temporary fixes to stop the limit problems consequences and secure the environment. What can you do right now?
4D - Determine and Verify Root Causes : Identify the true root cause.
5D - Choose and Verify Permanent Corrections : Develop and test long-term and reliable solutions.
6D - Implement and Validate Corrective Actions : Put your plan into action and ensure it works.
7D - Prevent Recurrence : Update processes and train your team to prevent future issues. How do you keep this from happening again?
8D - Congratulate the Team : Celebrate your success, document and share lessons learned.
A3 method
A3 problem solving uses a structured, one-page format to document the problem-solving process, encouraging clear communication and collaboration.
Background : Provide context for the problem.
Current State : Describe the current situation. What's happening now?
Goals/Targets : Set clear and measurable goals.
Root Cause Analysis : Identify root causes.
Countermeasures : Develop specific solutions to face the problem.
Implementation Plan : Outline the steps for implementation. Who does what, and when?
Follow-up : Monitor progress and make adjustments.
QRQC - Quick Response Quick Control
QRQC is an agile and action-oriented approach used to resolve issues in real time.
Quick response :
Identify and describe the problem.
Act quickly to contain and secure the problem. What can you do right now ?
Quick Control :
Identify root causes.
Implement long-term solutions. How do you fix the problem for good?
Standardize and Update processes to reflect the changes.
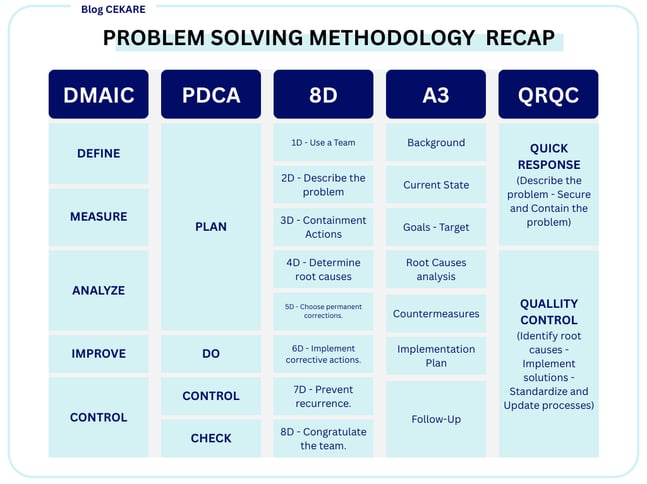
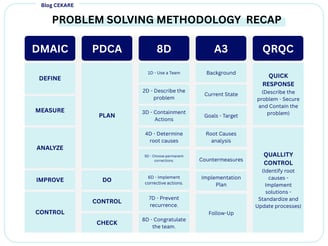
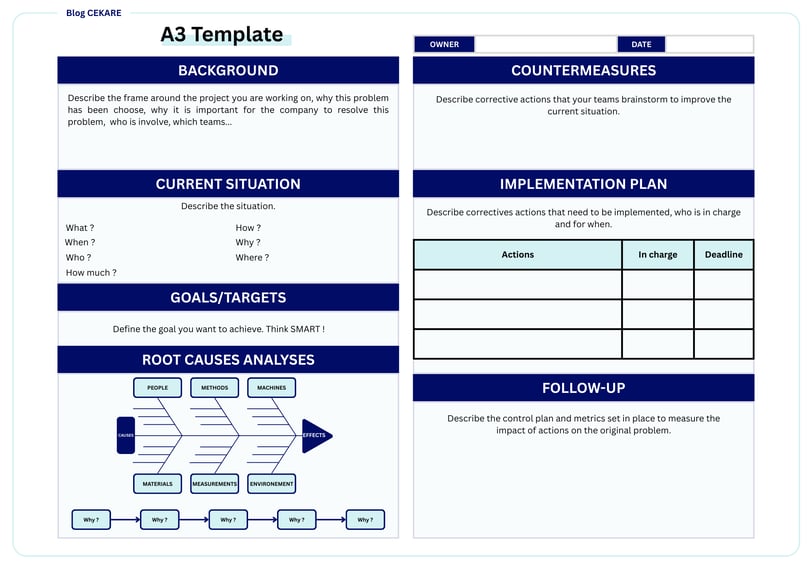
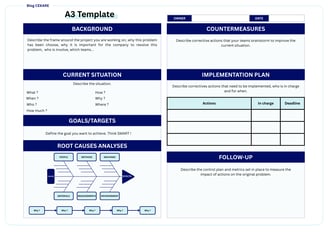
Choosing the right problem-solving methodology.
With so many methodologies to choose from, how do you pick the right one? Consider these factors:
Complexity: Problems can be really simple to fix, ideally with PDCA, whereas complex ones will be more easy to handle with 8D.
Urgency: Are you facing a situation that needs a quick fix ? Consider using QRQC to help you address urgent issues swiftly. Are you looking for improvement with long term impact ? Consider DMAIC.
Resources: Short on time or personnel? PDCA can be implemented with minimal resources.
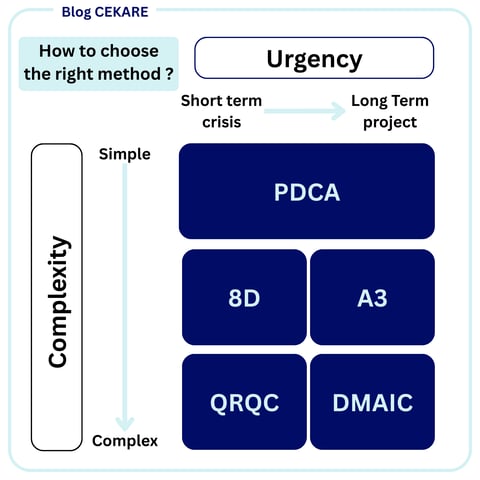
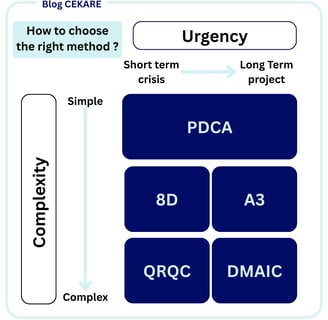
Tools to use in problem-solving.
All methodologies will lead you step by step to implement a new mindset within your company. To help you to control even more efficiently each problem solving step, You can use tools designed to be easily used by everyone, even without strong lean knowledge.
5W2H (Who - What - When - Where - Why - How - How much)
When faced with a problem, start by answering these seven key questions. This approach ensures you have a comprehensive understanding of the issue from all angles.
Who - "Who is affected? Who identified the problem?"
What - "What is the issue? What happened?"
When - "When does it occur for the first time? Since when?"
Where - "Where does it happen?"
Why - "Why is it happening?"
How - "How does it impact operations?"
How much - "How much does it cost?"
Pareto Analysis
Pareto Analysis is based on the 80/20 rule, which suggests that 80% of problems are caused by 20% of the causes. By using a Pareto chart, you can identify the most significant factors contributing to a problem. This tool helps you focus on your efforts on the vital few issues that will yield the most significant improvements, ensuring that your problem-solving efforts are efficient and impactfull.
Ishikawa Diagram (Fishbone Diagram - 6M)
The Ishikawa Diagram, also known as the fishbone diagram or Cause and Effect diagram, is a visual tool that helps you identify and map out potential causes of a problem. By categorizing causes into areas such as people, methods, machines, materials, measurements, and environment, you can systematically brainstorm and identify root causes. This diagram encourages a structured approach to problem-solving, making it easier to see the relationships between different factors.
SMART
Setting SMART objectives ensures that your problem-solving efforts are focused and aligned with organizational goals. SMART stands for Specific, Measurable, Achievable, Relevant, and Time-bound. For example, setting a goal to "Reduce defect rate by 20% within the next quarter" provides a clear target that guides your actions and helps you track progress effectively.
5 Whys
The 5 Whys technique is a simple yet powerful tool for root cause analysis. By asking "why" five times, you can uncover the underlying issues rather than just addressing the symptoms. This technique helps you dig deeper into the problem, ensuring that you identify and address the root cause, leading to more sustainable solutions.
Prioritization Matrix
When faced with multiple potential solutions, a prioritization matrix helps you determine which actions to take first. By evaluating solutions based on criteria such as impact, effort, and feasibility, you can score each option and prioritize them accordingly. This ensures that you focus on the most effective solutions that will yield the greatest benefits.
Action Plan
An action plan outlines the steps required to implement corrective actions. It specifies who will do what, by when, and with what resources. By developing a detailed action plan, you ensure accountability and clarity in the implementation process, making it easier to track progress and achieve your goals.
Control Plan
A control plan is essential for sustaining improvements. It involves monitoring key metrics and making adjustments as needed to ensure that the improvements are maintained over time. By setting up a monitoring system and establishing a process for reviewing and adjusting the improvements, you can prevent problems from recurring and drive continuous improvement.
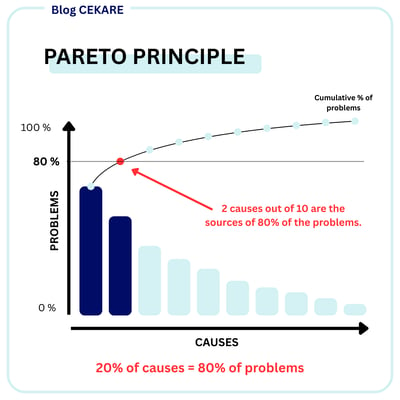
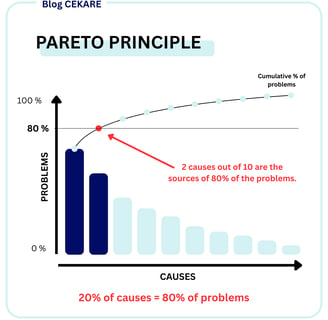
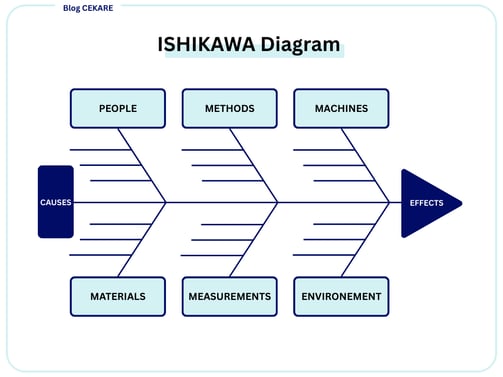
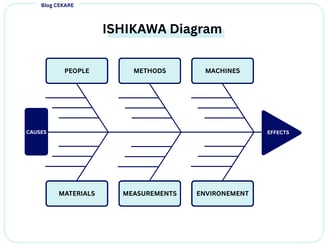
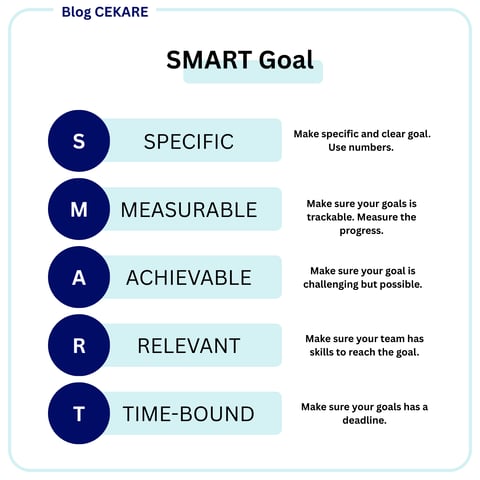
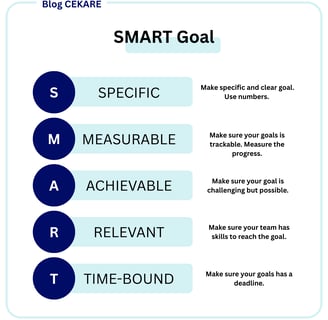
Conclusion about Problem Solving.
Problem-solving in lean management is more than just fixing issues; it's about creating a culture of continuous improvement. By embracing structured methodologies and leveraging powerful tools, you can transform challenges into opportunities for growth. Imagine the potential for your organization when every problem becomes a stepping stone to greater efficiency and innovation.
Ready to take your problem-solving skills to the next level? Contact us to learn more about how our expertise in lean management and problem-solving methodologies can drive your business forward. Let's work together to turn your challenges into success stories.
CEKARE
Boost your operational and industrial performance.
Mail : contact@cekare.eu
Phone : +370 663 58 502
© 2025. All rights reserved.