Blog CEKARE #3
MUDA - THE 7 WASTES
By Baptiste CARRE, 26/03/2025.
Time to read : 5 min
In today's fast-paced business environment, efficiency is the name of the game. But did you know that hidden inefficiencies, known as MUDA, could be holding your company back? Let's dive into this concept and explore how identifying and eliminating MUDA can transform your operations and boost productivity.
SUMMARY
Understanding MUDA: Origins and Types
The concept of MUDA, which translates to "waste" in Japanese, has its roots in the Toyota Production System (TPS), developed in the 1950s. During this era, Toyota faced severe resource constraints and needed to innovate to survive. The company's engineers and managers developed a system focused on eliminating waste and maximizing value, which later evolved into Lean Manufacturing. This methodology has since been adopted globally across various industries, from manufacturing to healthcare and beyond.
MUDA is categorized into two types:
Type 1 : These are non-value-added but necessary activities. They include tasks required by regulations or standards that cannot be eliminated but should be minimized. For example, compliance documentation is essential but doesn't directly add value to the end product. The goal is to streamline these processes to reduce the time and resources they consume.
Type 2 : This is pure waste with non-value-added, which can and should be eliminated entirely. It includes activities that do not contribute to the final product or service and can be removed without any adverse effects.
To identify and eliminate MUDA, it's essential to understand its seven forms. Use the acronym TIMWOOD to remember them:
Transportation
Inventory
Motion
Waiting
Over-processing
Overproduction
Defects
Each of these represents a different way that waste can infiltrate your processes, leading to inefficiencies and increased costs. By understanding and addressing these types of waste, you can significantly improve your operations.
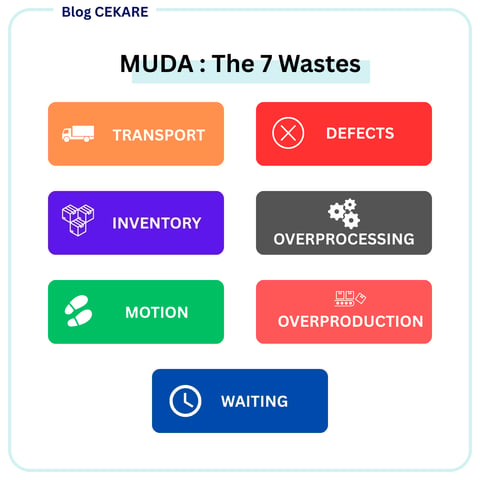
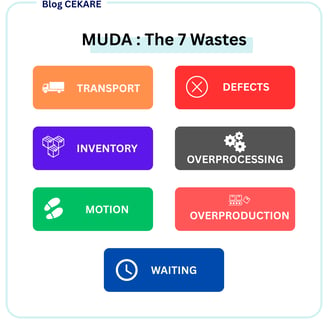
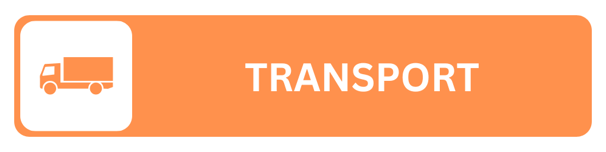
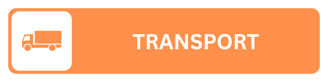
The Seven Types of MUDA: Uncovering Hidden Inefficiencies.
Let's explore each type of MUDA in detail, describing their impact and providing clear examples for both industry and services.
Transportation waste involves the unnecessary movement of materials, information, or people. This excess movement increases lead time and the risk of damage or loss, leading to higher costs and potential delays.
Examples : Moving raw materials multiple times before they reach the production line. Excessive transfer of documents between departments, leading to delays and miscommunication.
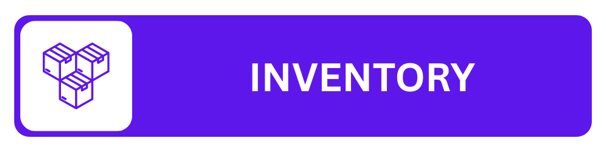
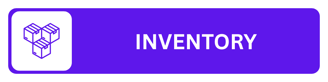
Excess inventory ties up capital and space, leading to higher storage costs and the risk of obsolescence. This excess stock not only takes up valuable space but also represents money that could be invested elsewhere.
Examples: A warehouse filled with unsold products, tying up capital and space. A service provider with excess supplies that are not being used, leading to wasted resources.
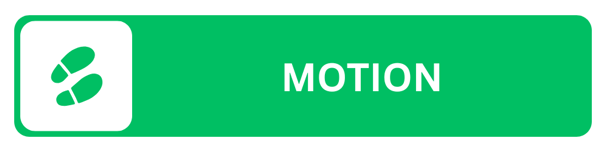
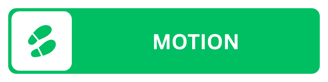
Unnecessary motion refers to the inefficient movement of workers or equipment within a process. This excess motion increases fatigue and reduces productivity, leading to longer lead times and higher labor costs.
Examples: Employees walking long distances to retrieve tools or materials due to an inefficient workspace layout. Staff moving between different offices to complete tasks that could be centralized.
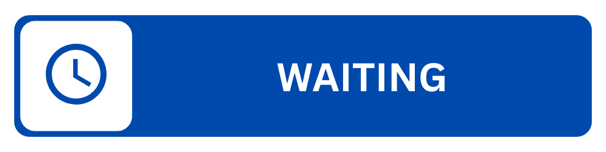
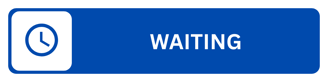
Waiting waste occurs when there is idle time where no value is being added. This could be machines or workers idling due to process delays or customers waiting in line for service. Waiting leads to longer lead times and reduced capacity, resulting in frustrated customers and lost revenue.
Examples: Machines idling due to a lack of raw materials or maintenance issues. Customers waiting in line at a bank or call center, leading to dissatisfaction.
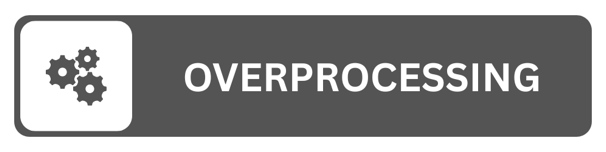
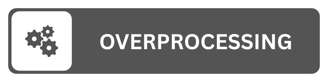
Over-processing involves adding more features, steps, or complexity than required by the customer. This extra work increases costs and lead time without adding value, leading to inefficiencies and wasted resources.
Examples: A manufacturer adding unnecessary features to a product that customers do not use. A report containing excessive details that no one reads, wasting time and resources.
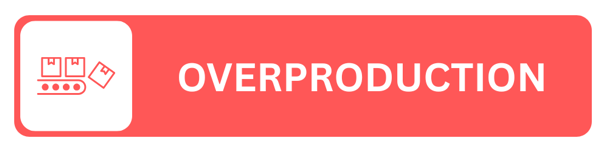
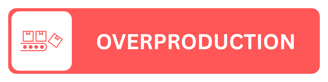
Overproduction occurs when more is produced than what is needed or before it's needed. This excess inventory leads to increased storage costs and the risk of obsolescence.
Examples: A factory producing 1,000 units daily when market demand is only 800 units. Preparing more food than needed for a catering event, leading to waste and increased costs.
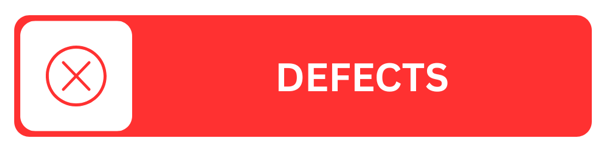
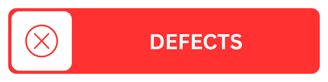
Defects are products or services that don't meet quality standards and require rework. This increases costs, lead time, and customer dissatisfaction, leading to lost revenue and damaged reputation.
Examples: A manufacturing line producing faulty products that need to be fixed or replaced. A software developer delivering a buggy application that requires extensive debugging.
Applying MUDA to Your Processes
Eliminating MUDA requires a systematic approach that involves identifying, analyzing, and addressing waste in your processes. Here's how you can apply the concept of MUDA to improve efficiency and productivity:
Identify MUDA : Map your processes and observe them in action to identify areas of waste. Engage your team to gather insights and identify pain points.
Analyze the Impact : Use data to quantify the impact of waste and perform root cause analysis to understand underlying issues.
Implement Solutions : Apply Lean tools like Kanban and Just-In-Time (JIT) to eliminate waste and improve efficiency. Make continuous improvement an ongoing effort.
Engage Your Team : Involve everyone in identifying and solving problems related to waste. Provide training on Lean principles to empower your team.
Monitor and Adjust : Track progress using KPIs and be prepared to adapt your strategies based on feedback and results.
Conclusion about MUDA
MUDA is a silent efficiency killer that lurks in every process. By understanding and eliminating these seven types of waste, you can transform your operations and achieve better results. Don't let hidden inefficiencies hold your company back. Take the first step towards a leaner, more efficient future today.
Ready to optimize your processes and boost your operations? Contact us to discuss how our consulting services can help you identify and eliminate MUDA in your organization. Let's work together to unlock your full potential!
CEKARE
Boost your operational and industrial performance.
Mail : contact@cekare.eu
Phone : +370 663 58 502
© 2025. All rights reserved.